RFID Medication Management & Tracking System
KitCheck simplifies RFID kit and tray management for over 900 hospitals and is the most trusted RFID medication tracking system in the market. As a full-workflow drug inventory management solution, KitCheck prevents waste, stockouts, and inaccuracies to improve patient safety and decrease unnecessary spend.
KitCheck’s hospital medication tracking system maximizes staff productivity with significantly faster restocking, recall mitigation, and shortage management across central pharmacies, ORs, and other drug distribution centers driving efficiency throughout your health system.
Complexities of Medication Management
Medication tracking for kits, trays, and high-cost drugs demands inventory management solutions that improve accuracy, streamline workflows, reduce waste, and maintain supply continuity.
The Solution:
RFID-Enabled Pharmacy & Hospital Medication Tracking
Stock Accurately and Efficiently
KitCheck is an automated RFID-enabled medication management system with 100% accuracy, every time. It uses a process that is 10x faster than manual medication inventory tracking alternatives.
Pharmacy staff can scan each used kit or tray in just seconds using the RFID scanning box, and immediately identify missing items, extra items, as well as expired and soon-to-be expired inventory. Simply restock according to the real-time summary, and scan again to confirm the replenished kit or tray is error-free. This simple, automated drug inventory management workflow maximizes the productivity of technicians and pharmacists, reducing overtime and improving staff satisfaction.
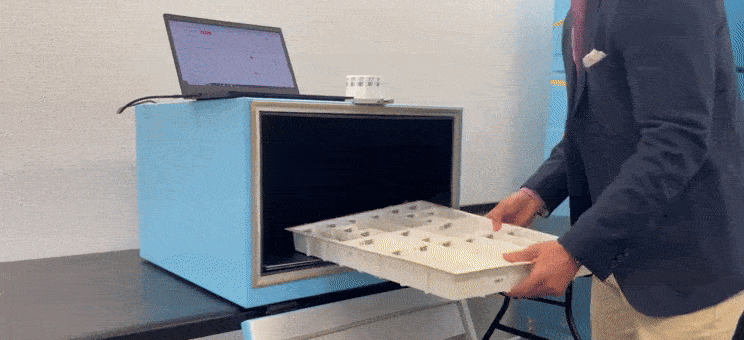
Simplify OR Anesthesia Restocking
Improve your OR medication restocking workflows, whether your hospital uses anesthesia workstations or non-automated anesthesia cabinets. Restock trays in the central pharmacy with our signature RFID scanning box or leverage the Mobile Pharmacy cart for a space-saving process that lets staff restock trays near the ORs and procedural rooms. Both medication delivery workflows ensure the same accuracy and efficiency that KitCheck provides for other types of RFID kits and trays, while preventing disruptive, burdensome stock-outs that frustrate providers and impact patient care.
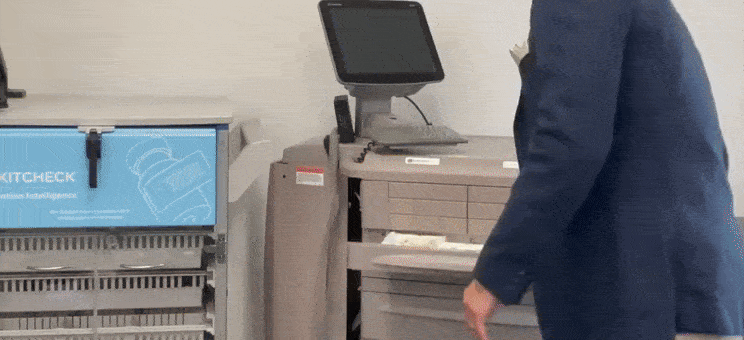
Reduce Waste and Optimize Inventory
Decrease unnecessary spend by reducing expirations and perfecting PAR levels. Hospitals can use KitCheck to track medication expirations and allocate inventory to ensure each unit is consumed prior to expiration, ultimately reducing waste by up to 92%. To optimize inventory KitCheck’s real-time, location-specific analytics reveal the required inventory levels required for each item in each kit or tray based on consumption trends, resulting in lower purchase quantities and hard-dollar savings.
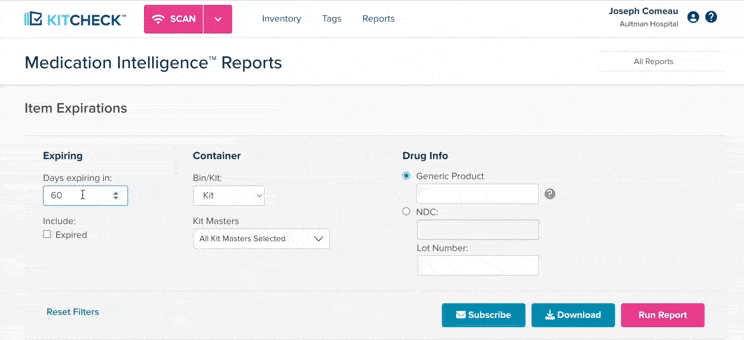
Mitigate Recalls and Shortages
Instantly pinpoint the location of unit-level inventory by lot number – down to a specific crash cart or anesthesia workstation. For recalls, this helps prevent patient safety risks and remove affected lots 33x faster than manually checking each kit and tray. KitCheck also provides recall alerts and flags the recalled inventory in your database. For shortages, identify specific products site-wide to efficiently reallocate inventory as needed, make appropriate substitutions, and set temporary PAR levels to manage limited inventory.
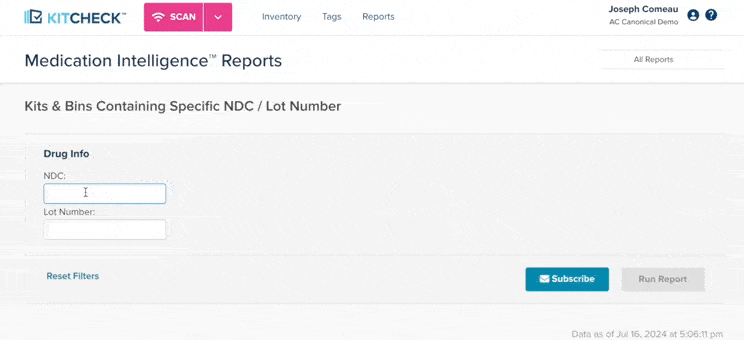
Track Critical Medications Anywhere
KitCheck can now function as a complete, end-to-end drug inventory management system for hospitals that lets you track your entire medication inventory outside of kits and trays.
KitCheck Anywhere uses KitCheck industry leading RFID medication tracking technology to monitor your health system’s most critical inventory across your existing refrigerators, shelves, and cabinets to see real-time stock-levels, expirations, and inventory movement. From central pharmacy and operating rooms to clinics and infusion centers, the KitCheck Anywhere RFID bins are flexible to any setting or drug type to track your high cost, refrigerated, or fast moving drugs.
Stock Accurately and Efficiently
KitCheck is an automated RFID-enabled medication management system with 100% accuracy, every time. It uses a process that is 10x faster than manual medication inventory tracking alternatives.
Pharmacy staff can scan each used kit or tray in just seconds using the RFID scanning box, and immediately identify missing items, extra items, as well as expired and soon-to-be expired inventory. Simply restock according to the real-time summary, and scan again to confirm the replenished kit or tray is error-free. This simple, automated drug inventory management workflow maximizes the productivity of technicians and pharmacists, reducing overtime and improving staff satisfaction.
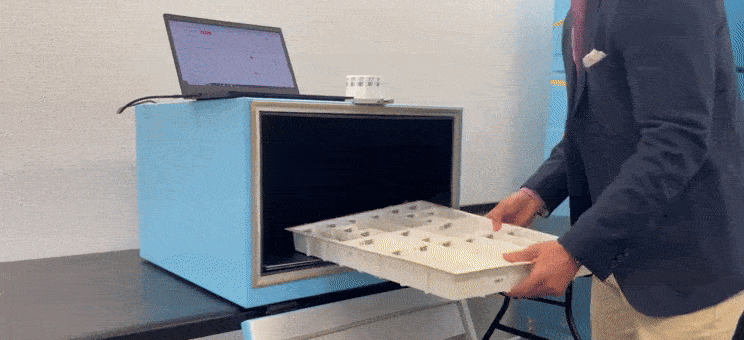
Simplify OR Anesthesia Restocking
Improve your OR medication restocking workflows, whether your hospital uses anesthesia workstations or non-automated anesthesia cabinets. Restock trays in the central pharmacy with our signature RFID scanning box or leverage the Mobile Pharmacy cart for a space-saving process that lets staff restock trays near the ORs and procedural rooms. Both medication delivery workflows ensure the same accuracy and efficiency that KitCheck provides for other types of RFID kits and trays, while preventing disruptive, burdensome stock-outs that frustrate providers and impact patient care.
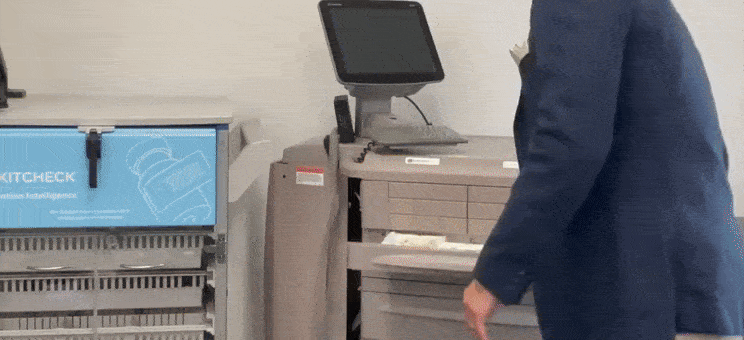
Reduce Waste and Optimize Inventory
Decrease unnecessary spend by reducing expirations and perfecting PAR levels. Hospitals can use KitCheck to track medication expirations and allocate inventory to ensure each unit is consumed prior to expiration, ultimately reducing waste by up to 92%. To optimize inventory KitCheck’s real-time, location-specific analytics reveal the required inventory levels required for each item in each kit or tray based on consumption trends, resulting in lower purchase quantities and hard-dollar savings.
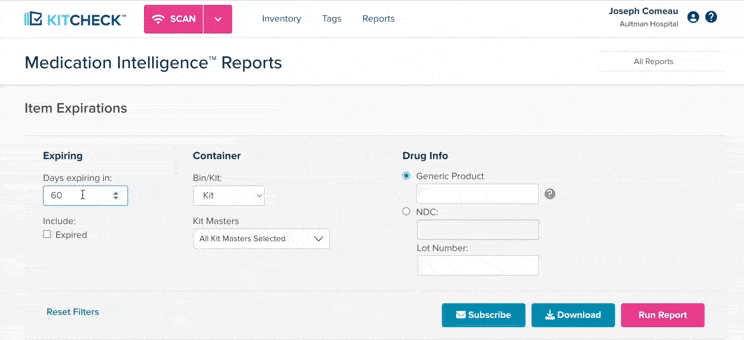
Mitigate Recalls and Shortages
Instantly pinpoint the location of unit-level inventory by lot number – down to a specific crash cart or anesthesia workstation. For recalls, this helps prevent patient safety risks and remove affected lots 33x faster than manually checking each kit and tray. KitCheck also provides recall alerts and flags the recalled inventory in your database. For shortages, identify specific products site-wide to efficiently reallocate inventory as needed, make appropriate substitutions, and set temporary PAR levels to manage limited inventory.
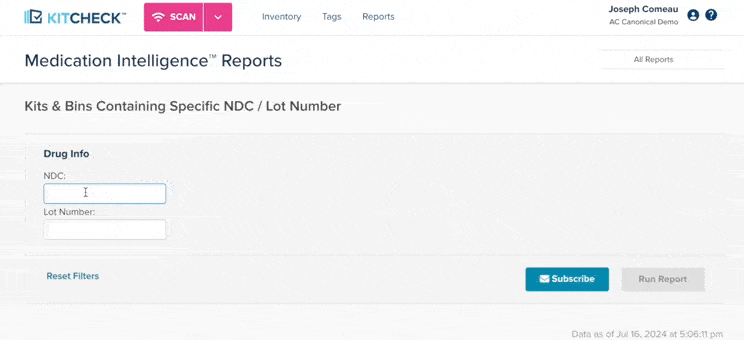
Track Critical Medications Anywhere
KitCheck can now function as a complete, end-to-end drug inventory management system for hospitals that lets you track your entire medication inventory outside of kits and trays.
KitCheck Anywhere uses KitCheck industry leading RFID medication tracking technology to monitor your health system’s most critical inventory across your existing refrigerators, shelves, and cabinets to see real-time stock-levels, expirations, and inventory movement. From central pharmacy and operating rooms to clinics and infusion centers, the KitCheck Anywhere RFID bins are flexible to any setting or drug type to track your high cost, refrigerated, or fast moving drugs.
100%
accurate restocking in kits and trays
10x
faster than manual restocking
85+
pre-tagged medications available
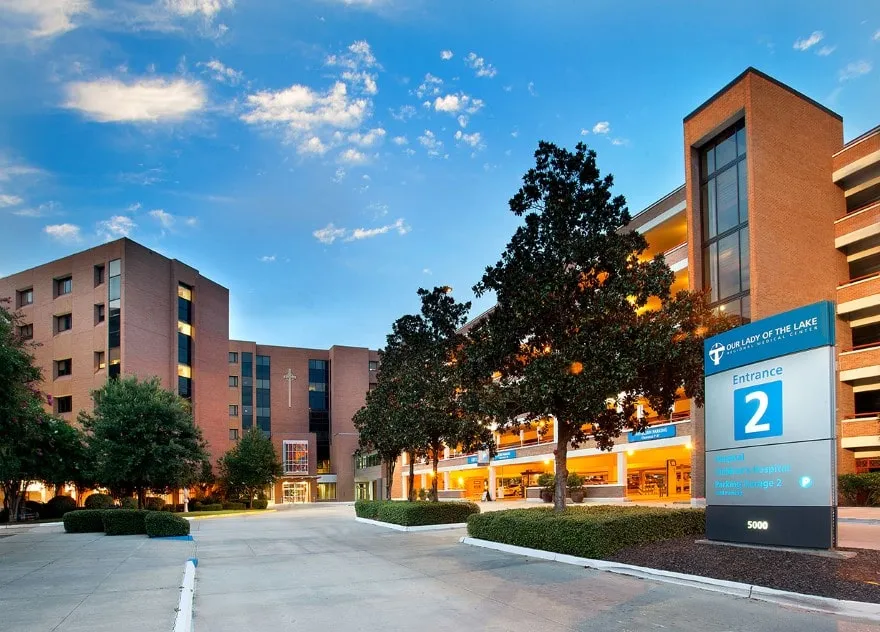
SUCCESS STORY
Our Lady of the Lake Medical Center
In recent years, the pharmacy team at Our Lady of the Lake Regional Medical Center identified a recurring challenge with operating room inventory: after medications were stocked in the anesthesia workstations (AWS), visibility of that inventory diminished.
By implementing RFID technology into OR inventory management in 2023, they were able to resolve this challenge, save 17 hours of staff time every week, reduce stockouts, increase patient safety, enhance regulatory readiness, and improve employee satisfaction.
What Our Customers Have to Say
“With KitCheck, the Anesthesia tray restocking process is 35% faster, but 100% better. There is a lot of value in having consistently correct restocking, both in staff efficiency and patient safety. KitCheck is delivering in both of those areas.”
Adrian Gonzales, PharmD, Director of Central Pharmacy Services
Want to learn more about KitCheck?
Request a demo to see KitCheck in action and discover how Bluesight can deliver value to your organization.
Schedule a Demo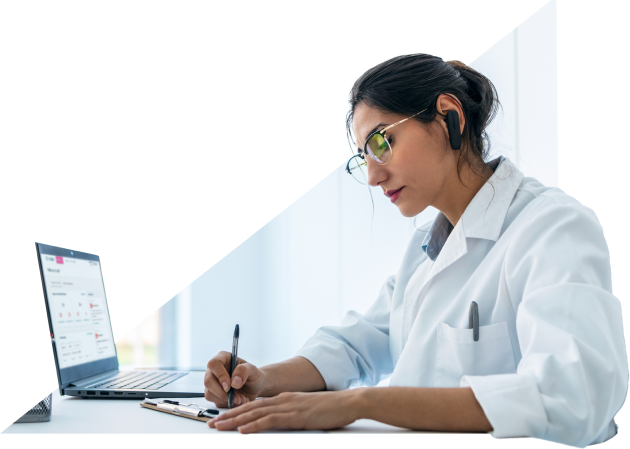